The transition towards renewable energy is among todays’ priorities, key in the Objective 7 of the Sustainable Development Agenda of the UN. Among the renewable energy types, the wind energy is very important: the earth atmosphere is the largest and most powerful thermodynamic engine, able to convert solar energy to air flow to a huge scale. Current conversion equipment based on rotating blades (windmills) is growing fast (about 95 GW/year, total installed capacity of 0.8 TW in 2021) but brings challenges, of which two are key: the efficiency of the drivetrain and the system reliability. With increasing output power approaching 15 MW, the drivetrain losses must be very tiny: each percent corresponds to a huge amount of heat to dissipate. The system reliability is essential because repairs and replacements of components in equipment at 100 m or more up in the air, often over a sea, are impractical and unaffordable.
The heat dissipated in the drivetrain shortens the lifetime of the system. Because of the large size (blades even longer than 100 m and bearing and gears with diameters in excess to a metre), the complexity of the geometry (blades, gears, …), the measuring instruments and techniques hardly catch up the technological demands.
The Met4Wind project has a comprehensive approach of the topic: from the measurement of key mechanical components with multi‑sensor techniques, to the evaluation of the surface state, to digital twins to monitor and predict the system state, to in‑line metrology in manufacturing rotating components. Within the project, the INRiM contributes to the study on multi‑sensor techniques and to the measurement of key components.
Contributing scientific sectors
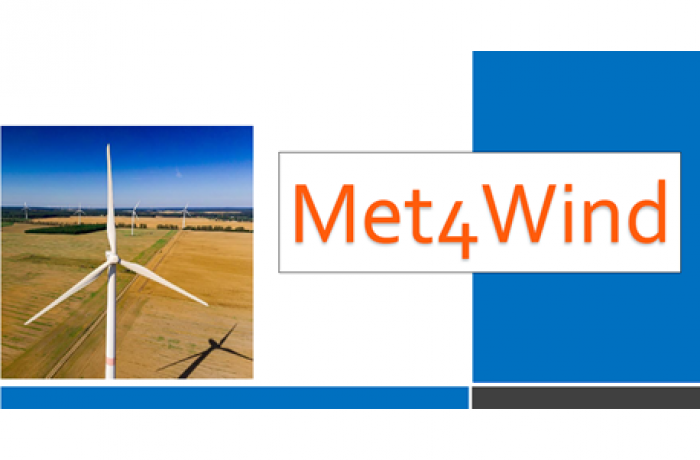